Optimizing Large Assembly Design in SolidWorks: Best Practices, Challenges, and Data Management
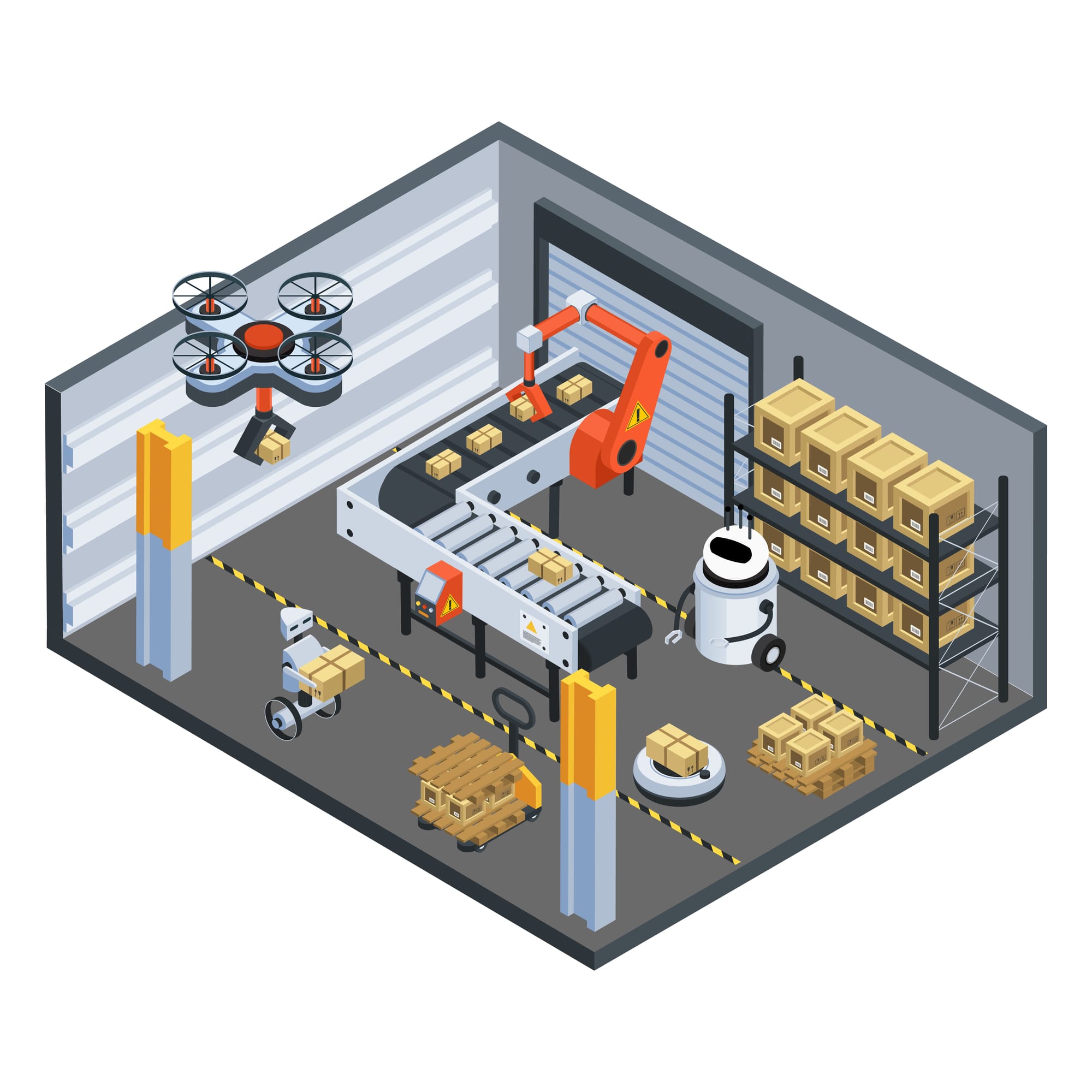
Introduction
In modern product design, handling large assemblies in Computer-Aided Design (CAD) software such as SolidWorks presents a unique set of challenges. As design complexity increases, so does the strain on system resources, leading to slower performance, decreased productivity, and potential project delays. The term "large assembly" in SolidWorks is not strictly defined by the number of components but is rather characterized by its demand on system resources and the extent to which it hampers productivity. This thesis explores the fundamental challenges of large assembly design in SolidWorks, best practices for optimizing performance, and the critical role of data management in maintaining efficiency.
Characteristics of Large Assemblies
Large assemblies typically possess two primary characteristics: (1) they exhaust system resources, and (2) they negatively impact productivity. These issues are often driven by several factors:
- Physical Size: Large assemblies often require complex layouts and precise positioning of numerous components, which places a significant burden on system memory and processing power.
- Component Complexity: Assemblies with many parametric relationships, mates, and complex geometry can further strain system performance, making it difficult to rebuild or modify parts efficiently.
- Geometric and Data Complexity: Imported data, extensive libraries, and routed systems can contribute to slow processing times. SolidWorks models that contain hundreds of components can become difficult to manage without efficient data handling methods.
While improving hardware can help alleviate performance issues, the primary cause of slowdowns in large assemblies often stems from poor modeling practices. According to studies, around 80% of performance issues in SolidWorks are user-controlled, stemming from inefficient software and data management practices, while only 20% are related to inherent software or hardware limitations.
Common Performance Issues in Large Assemblies
Large assemblies exhibit several common performance issues that degrade the user experience:
- Long Opening, Closing, and Saving Times: Complex assemblies take longer to load and save due to the large number of components, references, and parametric relationships that need to be processed.
- Slow Rebuild Times: Modifications to parts or assemblies require significant time for the system to recalculate geometry and parametric relationships.
- Sluggish Drawing and Viewing: Manipulating large assemblies—such as rotating, panning, or zooming—can become sluggish as the system struggles to keep up with the visual and computational demands.
- Mate Management: Poorly managed mates and over-reliance on in-context features can severely slow down assembly performance.
Best Practices for Large Assembly Design in SolidWorks
To mitigate these challenges, SolidWorks users must adopt a set of best practices that optimize the design process. These strategies aim to reduce system strain, improve efficiency, and ensure smooth collaboration among design teams.
1. File and Data Management
Effective file management is critical when dealing with large assemblies. Ensuring that all design team members have access to the most current version of files, while preventing unauthorized overwriting, is essential to maintaining data integrity. The use of Product Data Management (PDM) systems is highly recommended to:
- Track revisions and versions of files
- Control user access
- Locate file dependencies
- Ensure files are stored locally to optimize performance.
2. Modeling Best Practices
Efficient modeling reduces the computational load on SolidWorks:
- Simplified Part Design: Use simplified geometry or parasolid bodies for library and purchased components to reduce the complexity of parts.
- Sub-assembly Organization: Break large assemblies into sub-assemblies to reduce the number of mates and interrelationships that need to be processed at the top level.
- Lightweight Components: Load assemblies in lightweight mode to avoid loading detailed geometry until necessary.
- SpeedPak: Use the SpeedPak configuration to simplify the assembly without sacrificing essential data for visualization or drawing.
3. System Settings and Configurations
Optimizing system-level settings in SolidWorks can significantly improve performance:
- Large Design Review: Use this mode when opening large assemblies to view the assembly without loading all details and geometry.
- Quick View and Lightweight Mode: Utilize these features to load minimal data for viewing or manipulation, saving on processing time.
4. Design Strategies
Planning ahead is crucial for managing large assemblies effectively:
- Skeleton Model Technique: Commonly used for large machinery, this method enables designers to visualize important interfaces at the sub-assembly level.
- Master Model Technique: Ideal for consumer products with complex surfaces, this approach allows designers to create components from a single, multi-body master model.
Data Management in Large Assembly Design
Efficient data management is a cornerstone of large assembly design. SolidWorks relies on a single-point database structure, meaning that all information is stored in individual files. Poor data management can lead to delays, lost data, and overwriting of files, which can be catastrophic in large projects.
1. Manual vs. Automated Data Management
In the absence of a PDM system, manual methods of file management are prone to errors. For instance, storing files in a central location without version control may lead to accidental overwrites, loss of data, and inefficiencies caused by opening files over a network. In contrast, PDM systems offer version control, revision tracking, and permissions management, ensuring that users access only the correct files and preventing data loss.
2. SolidWorks PDM Solutions
SolidWorks provides several PDM solutions:
- SolidWorks Workgroup PDM: Designed for small to medium-sized teams, this system offers revision control, workflow management, and permission-based access to files.
- SolidWorks Enterprise PDM: Suitable for large teams or multi-site organizations, this system uses SQL databases and file replication to ensure fast access to data while maintaining version control across different locations.
3. The Importance of a Data Management Strategy
Without a proper data management system, large assembly design can become chaotic. To prevent costly errors and delays, it is essential to have a well-documented and enforced data management strategy. This includes deciding how files will be named, how revisions will be tracked, and how in-context relationships will be managed.
Conclusion
Large assembly design in SolidWorks poses significant challenges due to the strain on system resources and the complexity of managing multiple components and data relationships. However, by following best practices in file management, modeling, and system configuration, users can optimize performance and maintain productivity. Adopting a robust data management strategy, including the use of PDM systems, is crucial for ensuring data integrity and preventing costly errors. Ultimately, successful large assembly design is the result of careful planning, disciplined execution, and efficient data management.
References
- Dassault Systèmes. (n.d.). SOLIDWORKS Large Assembly and Drawing Performance. Retrieved from solidworks.com
- Dassault Systèmes. (2023). Optimizing Performance in Large Assemblies. SolidWorks Technical Documentation.
- Dixon, M. (2019). Best Practices for Managing Large Assemblies in SolidWorks. Retrieved from cadalyst.com
- FEA Training Consultants. (2021). Managing Large Assembly Performance in SolidWorks. Retrieved from featc.com