Producing perfect products.
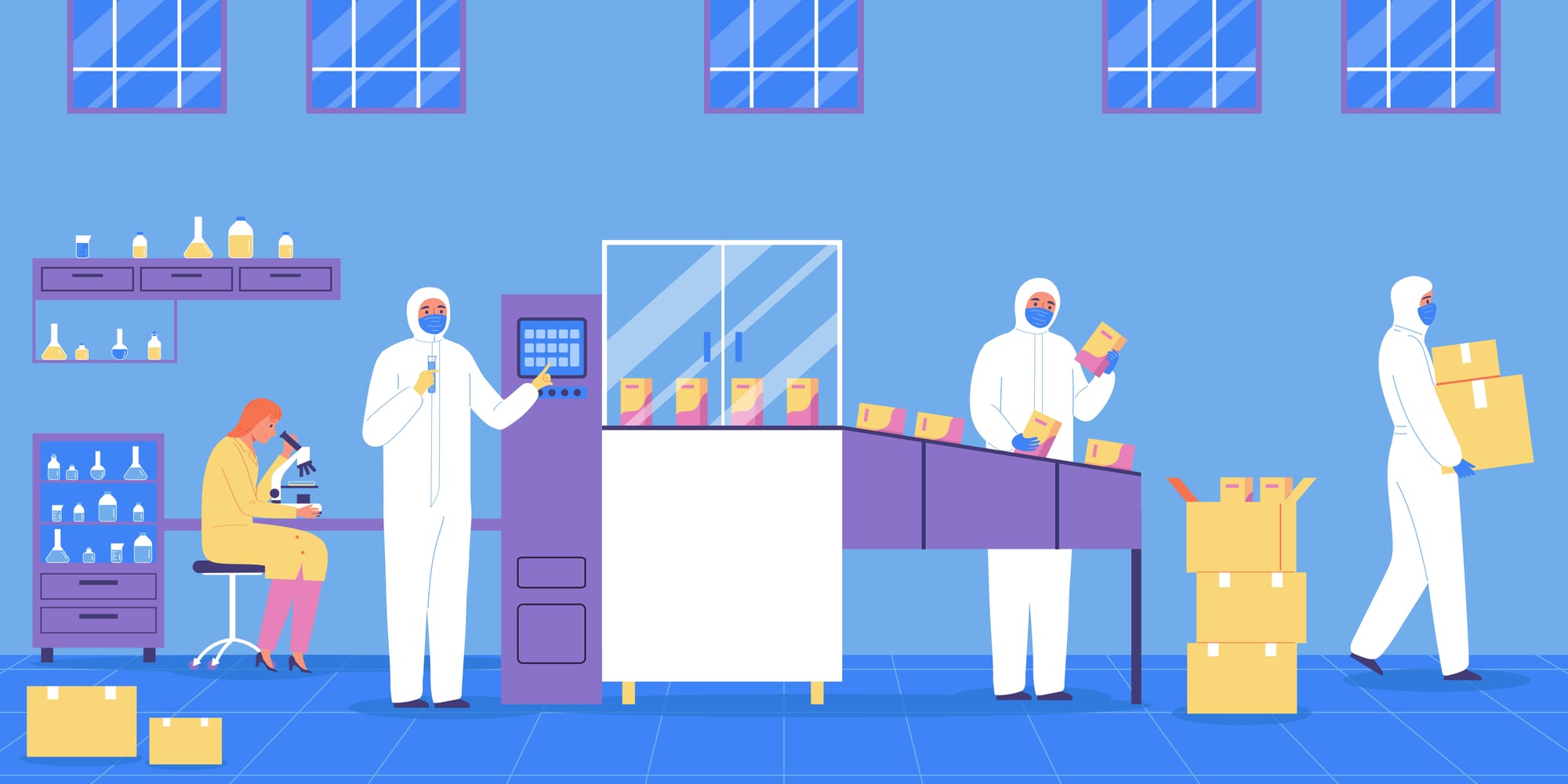
When it comes to the manufacturing industry, ensuring high-quality products should be the top priority for any business. The success of a brand or product relies heavily on the quality of the items produced, as customers are more likely to purchase products that meet high standards. With this in mind, it's crucial to implement a zero-defect manufacturing process to prevent any quality issues that may potentially lead to a loss of customers. Our informative and helpful video will guide you through the steps necessary to improve your manufacturing processes by utilizing this approach, ultimately ensuring that your products meet the highest possible standards.
Zero Defect Manufacturing
In order to achieve Zero Defect Manufacturing, it is vital to instill in all employees the understanding that every single aspect of their work is essential in ensuring that the final product is absolutely free from any kind of defects. This is a principle that has been emphasized by the late Philip B. Crosby, a renowned scholar who, in his book 'Quality is Free', highlighted the potential losses that may arise from defects in products. The ultimate goal of Zero Defect Manufacturing is to improve the manufacturing process to the point where there is no possibility of any defects in the final product.
The attainment of Zero Defect Manufacturing requires a change in perception and an unwavering pursuit of perfection. It is also essential for employees to understand the potential losses that may arise from poor quality products, as this knowledge is a key motivator for them to work towards achieving zero defects. In addition, anticipating future problems and taking proactive measures to address them is a crucial aspect of this approach.
To better understand the importance of zero defects, consider the example of a car's brakes. The brakes are a safety-critical component, and if they are not working properly, the customer expects the manufacturer to fix the issue promptly and effectively. By striving for zero defects, companies can better meet the expectations of their customers, bridging the gap between what they desire for themselves and what they offer to their customers. This not only leads to higher levels of customer satisfaction but also helps to establish the company's reputation for reliability, quality, and trustworthiness.
Implementation of Zero-Defect Manufacturing Process
In order to minimize the occurrence of defects, it is recommended to take preventive measures rather than waiting for them to manifest and then attempting to correct them. Detecting defects at an early stage provides an opportunity to rectify the issue before it escalates and causes more significant problems.
For example, if you observe that the brake shoe of your bike is not performing optimally, it is advisable to replace it promptly instead of waiting for it to completely malfunction, which could result in a hazardous accident. By taking preventive measures, you can save time and avoid potential risks that may arise from neglecting defects.
Quality to meet customer requirements
The primary objective of any product should be to cater to the needs and expectations of the customer. This is especially true when it comes to ink pens, where a local brand might offer superior quality than an expensive gold-plated pen that leaves ink marks while writing. In such scenarios, customers tend to lean towards the local brand, as it meets their requirements without any issues. Another perfect example of customer-centricity is CarboMedics, a company that specializes in producing medical equipment, including an artificial valve. They take a zero-defect approach in their manufacturing process, ensuring that their product fits perfectly the first time, and thus, instilling confidence in their customers. All in all, companies should prioritize customer satisfaction by creating products that cater to their specific needs, leading to long-lasting relationships with their customers.
Change in working behavior
It is highly recommended that you, along with your top management, employees, and workers, adopt the zero-defect management process approach in order to enhance the overall working behavior. This approach is aimed at minimizing the occurrence of defects and errors, thereby ensuring a high level of quality in the final product or service. By embracing this methodology, you can ensure that all aspects of your business operations are aligned towards achieving the ultimate goal of providing exceptional value to your customers. With everyone in the organization working towards the same objective, you can create a culture of excellence that will drive your business forward towards success.
Quality check to be mandatory
Ensuring the quality of every product is a vital aspect of the production process that cannot be overlooked. To achieve this, it is imperative that a mandatory quality check is conducted at every stage of production before the product leaves the factory. This process is crucial in identifying any defects that may exist and correcting them promptly to prevent any potential issues down the line. In addition, implementing self-testing mechanisms is highly recommended to facilitate the process further. Furthermore, it is equally important for team members to review each other's work and offer guidance where necessary to ensure that the desired outcome is achieved. In summary, maintaining high-quality standards is a team effort that requires diligence and attention to detail at every step of the production process.
Skilling and training
Ensuring that your factory workers possess the necessary skills and knowledge is an essential aspect of maintaining a smooth and error-free operation. There are several effective methods that you can employ to achieve this goal.
One approach is to organize regular training sessions for your employees. These sessions can cover a range of topics, from basic safety protocols to more advanced technical skills. Additionally, displaying training guides on the walls of your factory can provide your workers with clear and concise instructions that they can refer to whenever they encounter difficulties.
Another useful training method is the One Point Lesson. This brief but practical lesson, typically lasting 10 to 15 minutes, is conducted by a senior team member. During the lesson, employees learn how to operate a specific machine with ease and accuracy. This approach is particularly effective for helping workers to quickly master new equipment and processes.
By implementing these training methods, you can improve the overall skills and productivity of your workforce. This, in turn, can help to streamline your factory's operations, reduce errors and downtime, and ultimately lead to greater success for your business.
Automation
The implementation of automation in various business processes has become increasingly essential due to its ability to minimize the occurrence of human errors. This is particularly important as errors can have significant negative impacts on a business's overall productivity and profitability. By automating tasks, businesses can improve their efficiency and ensure that processes are carried out in a consistent and accurate manner, leading to improved outcomes and increased customer satisfaction.
Evaluation
In order to assess the effectiveness of your company's zero defect manufacturing process, there are a variety of tools at your disposal. These tools will enable you to determine whether your production is efficient, whether there is minimal wastage, and if the quality of your products has improved. Some of these tools include Total Productive Maintenance (TPM), Total Quality Management (TQM), Service Quality Measurement (SQM), Six Sigma Quality (SSQ), and Poka Yoke.
TPM is a tool that is used to decrease cycle time, increase production, and decrease the occurrence of defects. To implement TPM, you can issue inspection cards to determine which machines need maintenance and whether they have already been inspected. Additionally, TPM forms are available to help you organize all the information.
TQM is a tool that ensures that the product process is executed correctly the first time, thereby eliminating quality issues. SQM involves asking customers to rate your product on reliability and their overall experience in-store or on the website.
SSQ aims to ensure quality checks at every step of the manufacturing process by creating a set of processes. Poka Yoke is a tool used for error prevention and is widely used in Japan. Workers receive an alert before committing a mistake, such as through an alarm system.
It is critical to maintain quality in the manufacturing process, as defects can lead to double expenses, including additional inspections, new materials, and re-engaging labor. Furthermore, poor quality can harm your brand image. Therefore, many companies now use zero defect tools in their manufacturing processes to maintain quality. If suppliers of parts fail to meet zero-defect standards, companies may refuse to take parts from them.
To achieve successful zero-defect manufacturing, it is important to focus on quality control by improving processes and closely monitoring production. By using these tools and constantly working to improve the manufacturing process, your company can ensure that it is producing high-quality products that meet the needs of your customers.