Zero Defect Manufacturing
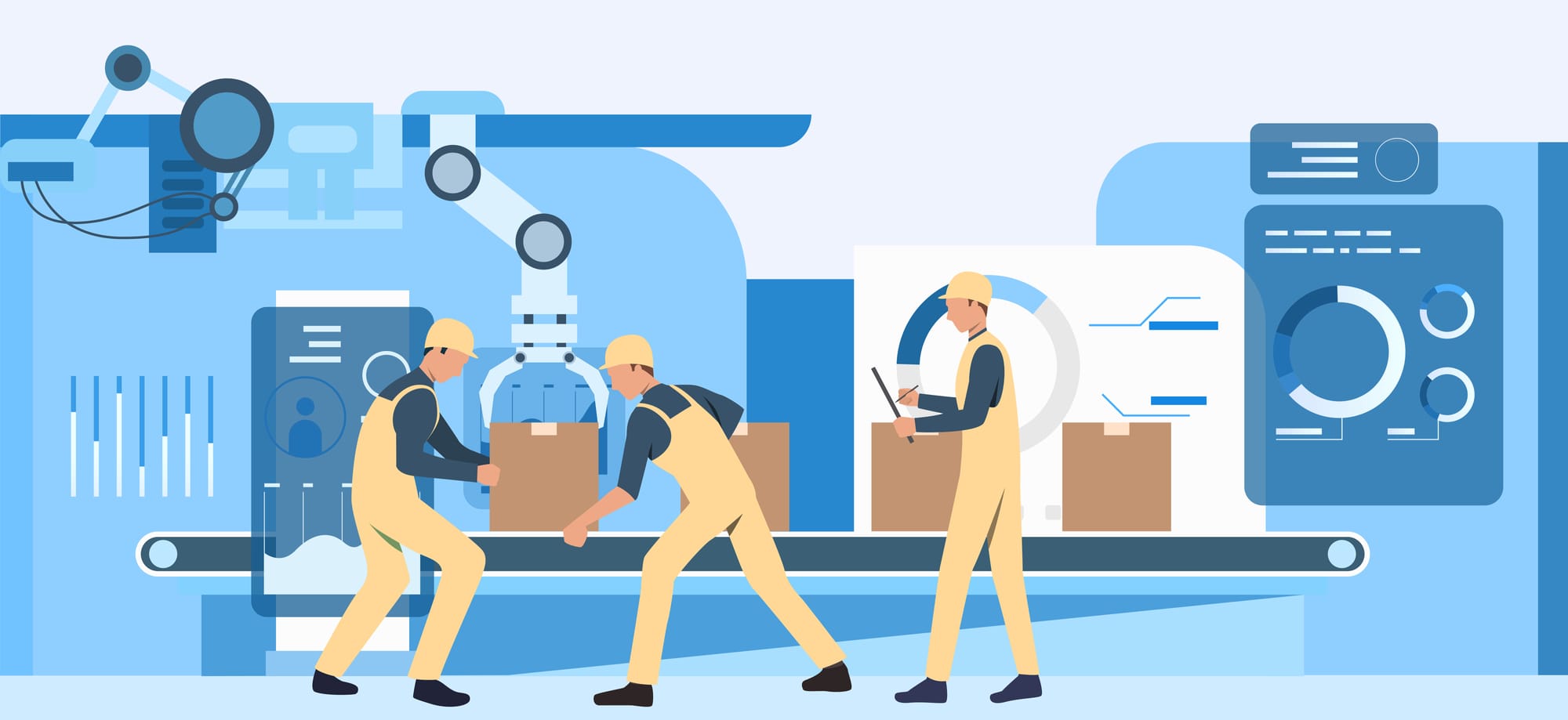
When implementing the zero-defect manufacturing process in your company, it's crucial to consider several factors. The success and reputation of a brand or product are intricately linked to its quality. This is because high-quality products are more likely to attract and retain customers. Therefore, prioritizing quality management is essential for any business.
Losing a customer due to quality issues can be detrimental to your business. It is always preferable to continuously improve your processes and manufacturing by embracing the principles of zero-defect manufacturing, which aims to minimize defects in the production process.
By adopting the zero-defect approach, you can ensure that your manufacturing processes are optimized to produce high-quality products consistently. This involves identifying and addressing potential sources of defects, implementing quality control measures, and continuously monitoring and improving the manufacturing process.
In the pursuit of Zero Defect Manufacturing, it is essential to create a work environment where every employee is deeply committed to upholding the highest standards of quality. Each individual should fully understand their role in ensuring that every product leaving the facility is free from any defects. This principle, as described by the well-respected scholar Philip B. Crosby in his influential book 'Quality is Free,' underscores the idea that even the smallest defect in a product can lead to significant financial losses. The primary objective of embracing this approach is to continuously enhance the manufacturing processes to achieve the ultimate goal of consistently producing flawless products.
Changing Mindset: It's imperative to cultivate a mindset that constantly aims for perfection and does not tolerate any compromise on quality.
Assessing Losses: It's crucial to meticulously identify and quantify the potential losses that could arise from the production of low-quality or defective products, including not just financial losses but also damage to the brand's reputation and customer trust.
Anticipating Issues: Taking proactive measures to anticipate and address any potential problems resulting from subpar quality is essential for maintaining high standards and preventing costly errors down the line.
For example, just as you would expect a car service center to effectively repair your brakes, adopting a zero-defect approach means providing the same level of reliability and excellence in your products and services. This approach aligns your personal standards with the high expectations you set for your customers, fostering a culture of unparalleled quality and customer satisfaction.
Implementation of Zero-Defect Manufacturing Process
When implementing a Zero-Defect Manufacturing Process, one key principle is that defect prevention is preferred to correction. It is crucial to identify and address defects at the earliest stage possible, as this saves time and resources. For instance, if a defect is discovered in the brake shoe of a bike, it is more efficient to replace it immediately rather than waiting for it to cause further damage, potentially leading to an accident.
Another important principle is ensuring that the quality of the product meets customer requirements. The ultimate goal of any product should be to satisfy the needs and expectations of the customer.
For example, when considering an ink pen, a local brand's pen that writes smoothly without any ink leakage may be preferred over a more expensive gold-plated pen that leaves ink marks while writing. In this case, the local brand's pen is considered higher quality as it fulfills the customer's requirements.
Similarly, in the medical industry, a company like CarboMedics applies the zero-defect approach in manufacturing their equipment, particularly their artificial heart valve. By adhering to this approach, they ensure that their product fits perfectly the first time and meets the specific requirements of the customer.
Change in working behavior
In order to successfully implement the zero-defect management process, it is crucial for the working behavior of all individuals within the organization to undergo a significant change. This includes not only top management but also all employees and workers. Embracing a mindset of continuous improvement and a commitment to achieving zero defects in all processes and outputs is essential for the success of this approach.
Quality check to be mandatory
Quality check is an essential step that must be mandatory at every stage before any product leaves the factory. The main objective of this process is to identify any defects as early as possible and take corrective actions. To ensure thorough quality checks, self-testing should be implemented, and all workers within the team should be responsible for checking each other's work and providing guidance to ensure that all products meet the required standards.
Skilling and training
In order to ensure the smooth operation of your factory, it is crucial to prioritize skilling and training for your employees. Training plays a vital role in equipping your workforce with the necessary knowledge and skills to perform their tasks effectively and minimize the risk of errors.
To facilitate training, consider organizing regular training sessions to familiarize employees with the operational processes. Additionally, displaying training guides in prominent areas within the factory can serve as a quick reference for employees who may need to clarify any aspect of their tasks.
Another effective training method to consider implementing is the "One Point Lesson." This method involves brief 10 to 15-minute practical sessions conducted by senior team members to demonstrate specific operational procedures or machine operations. This hands-on approach can significantly enhance employees' understanding of how to operate machinery and carry out tasks effectively.
Automation
The majority of errors are caused by humans rather than machines. Therefore, it is crucial to automate processes in order to reduce the occurrence of mistakes.
Evaluation
In order to assess the effectiveness of the zero defect manufacturing process in your company, it is important to utilize various tools to gauge the efficiency of production, minimize wastage, and enhance product quality. One such tool is Total Productive Maintenance (TPM), which is employed in production processes to reduce cycle time, boost production output, and minimize defects. TPM involves the use of inspection cards to track machine inspections and identify maintenance needs for each machine.
Don't worry, I've got the text you provided. Here's the revised version:
TPM forms, which are available, can assist you in effectively organizing all the necessary information.
- Total Quality Management (TQM): This tool is utilized to ensure that the product's manufacturing process is executed accurately the first time, thus avoiding any quality issues.
- Service Quality Measurement (SQM): This process involves gathering customer feedback to evaluate the product's reliability. Customers can rate their in-store or online experiences, as well as the assistance they received from customer service representatives over the phone.
When customers provide ratings on various parameters, you can use this feedback to identify areas where mistakes may have occurred.
Six Sigma Quality (SSQ) is a tool aimed at ensuring quality checks are implemented at every stage by streamlining processes.
Poka Yoke is a technique used for mistake-proofing and error prevention, commonly employed in Japan. It involves creating processes that provide alerts, such as through an alarm system, to workers before they make a mistake.
Quality Measured in Terms of Money
Maintaining high product quality is crucial for businesses, as it directly impacts financial costs and customer satisfaction. When a product is found to have defects, it requires additional inspection, rework with new materials, and extra labor, leading to increased expenses. Moreover, dissatisfied customers can further harm a company's reputation and lead to financial losses. For instance, in 2019, a significant number of cars were recalled in India due to airbag issues, affecting major brands like Maruti, Ford, and Hyundai. Consequently, these companies suffered financial losses and damage to their brand image.
To mitigate these risks, many companies have adopted zero-defect manufacturing processes, using tools and techniques to ensure products are free from defects. Additionally, companies have stringent requirements for their parts suppliers to maintain the same level of quality control. The entire process from production to delivery is critical, and companies are focusing on improving their processes and implementing effective monitoring and quality control measures to achieve successful zero-defect manufacturing.